Introduction
In industrial applications requiring precision, efficiency, and longevity, choosing the proper bearing type is vital. Angular contact bearings have become a popular choice in a variety of industries due to their ability to manage complex load requirements. These bearings are engineered to withstand both radial and axial loads, making them excellent for high-speed and precision applications.
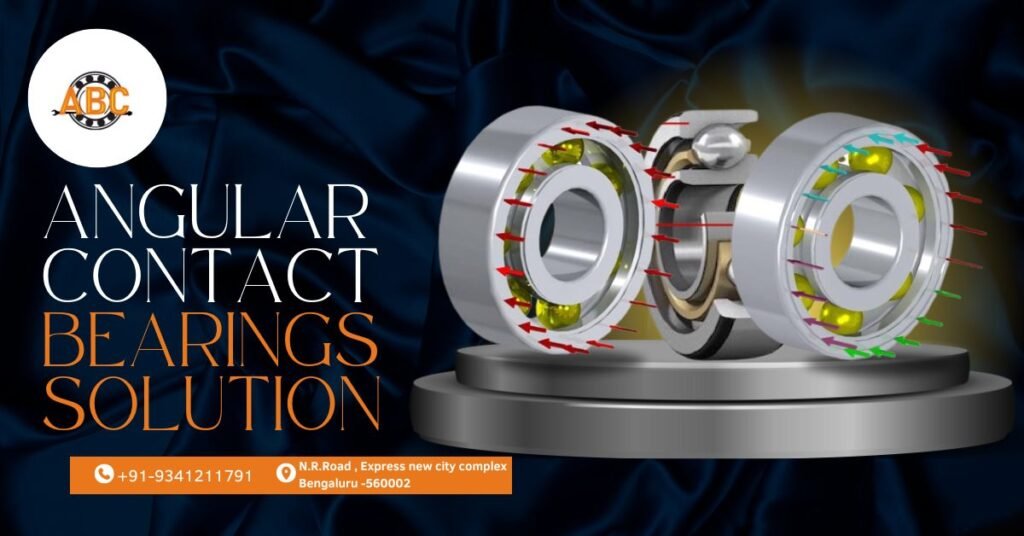
This blog explores angular contact bearings, their working principles, advantages, applications, and why they are an optimal solution for complex load conditions.
Understanding Angular Contact Bearings
Angular contact bearings differ from standard radial ball bearings in their unique design, which enables them to support both axial and radial loads. The inner and outer raceways are offset relative to one another, allowing them to sustain high axial loads in one direction while maintaining high rotational speed and rigidity.
Types of Angular Contact Bearings
There are various types of bearings, each designed to meet specific industrial needs:
- Single-Row Angular Contact Bearings: These bearings withstand axial loads in one direction and require a corresponding bearing to counteract the load.
- Double-Row Angular Contact Bearings: These bearings are perfect for applications requiring bidirectional axial support since they can manage axial loads in both directions.
- Four-Point Contact Bearings: These specialized bearings can handle axial loads in both directions with a single bearing, reducing the need for additional components.
- Matched Pair Angular Contact Bearings: These are preloaded pairs of bearings designed for high precision applications that require high stiffness and reduced deflection.
Key Advantages of Angular Contact Bearings
This offer several benefits that make them suitable for high-performance applications:
- High Load-Carrying Capacity: The fact that these bearings are able to withstand high axial and radial loads makes them appropriate for applications that are very demanding.
- Enhanced Rotational Speed: Their design minimizes friction, enabling smooth and high-speed rotation.
- Superior Precision and Rigidity: Because they are preloaded, they don’t deflect much when put under stress, which makes them ideal for uses that need pinpoint accuracy.
- Versatility: Available in different configurations and materials, they can be tailored to various industrial needs.
- Durability and Longevity: Angula contact bearings are engineered to endure severe environments and extensive usage due to their high-quality construction.
Applications of Angular Contact Bearings
Because of their high performance and reliability, bearings are used in various industries and applications:
1. Aerospace Industry
In aerospace applications, precision and reliability are paramount. Angular contact bearings serve in aircraft engines, landing gear, and control systems due to their ability to handle high speeds and complex loads.
2. Automotive Industry
Modern automobiles necessitate efficient bearing solutions for transmissions, wheel hubs, and suspension systems. Angular contact bearings assist these crucial components with their longevity and high load capacity.
3. Machine Tools and Robotics
High-precision machinery, such as CNC machines and robotic arms, depend on bearings for smooth operation, minimal vibration, and precise movement.
4. Medical Equipment
In medical applications like CT scanners and surgical robots, the necessity for precision and dependability renders bearings an optimal selection.
5. Industrial Pumps and Compressors
These bearings provide stability and efficiency under high-speed and high-load conditions, making them widely used in pumps and compressors.
Selecting the Right Angular Contact Bearing
Selecting the suitable angular contact bearing for a particular application relies on multiple considerations:
- Load Requirements: Evaluate the radial and axial load requirements of your application to identify the most suitable bearing type.
- Speed Considerations: High-speed applications require bearings with optimized lubrication and low-friction designs.
- Operating Environment: Temperature, humidity, and exposure to contaminants influence the choice of materials and lubrication.
- Preload and Clearance: Appropriate preload guarantees elevated stiffness and reduces play in precision applications.
- Bearing Arrangement: Single-row bearings may necessitate coupling, whereas double-row or four-point bearings can offer bidirectional support.
Installation and Maintenance Tips
In order to get the most out of bearings in terms of their performance and lifespan, it is vital to execute correct installation and maintenance:
- Correct Mounting Techniques: Use precision tools and follow manufacturer guidelines to ensure proper alignment and preload.
- Regular Lubrication: High-quality lubricants reduce friction and wear, ensuring smooth operation.
- Monitoring for Wear and Damage: Periodic inspections help detect early signs of wear, misalignment, or contamination.
- Proper Storage: Bearings should be stored in a clean, dry environment to prevent corrosion and contamination.
Conclusion
Angular contact bearings offer an effective and dependable option for situations necessitating the management of intricate loads. Their adaptability, exceptional accuracy, and resilience render them a crucial element in sectors spanning aircraft to manufacturing. By choosing the appropriate bearing type and adhering to regular maintenance protocols, enterprises can improve the efficiency and durability of their gear.
At Accurate Bearing, we offer a wide range of high-quality angular contact bearings to meet the needs of various industries. Contact us today to find the perfect bearing solution for your application.